Sharpen Corner Wooden Moulding Like a Pro with These Simple Tips
Wooden moulding is a fantastic way to enhance the aesthetics of interior spaces, providing a polished and professional look to walls, doors, and windows. However, achieving sharp, clean corners is essential for a seamless finish. Whether you’re installing crown moulding, baseboards, or chair rails, knowing how to sharpen corner wooden moulding will elevate your craftsmanship.
This guide will walk you through the best tips and techniques for achieving precise, professional-looking corners in your woodworking projects.
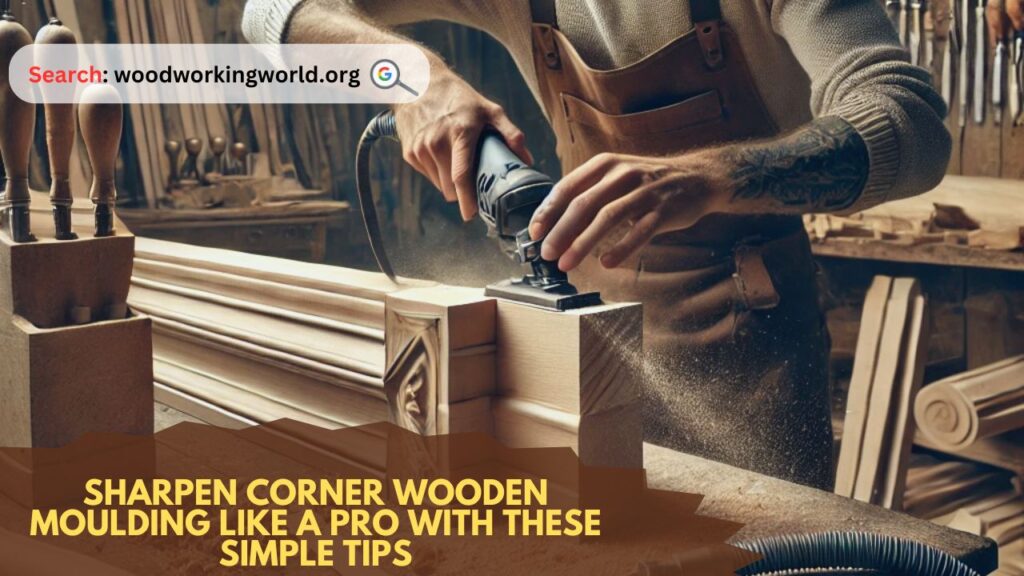
Why Sharp Corners Matter in Wooden Moulding
Sharp, well-defined corners are critical for the following reasons:
- Aesthetic Appeal: Clean corners create a polished and high-quality look.
- Structural Integrity: Properly joined corners are more durable and less prone to gaps or shifting.
- Seamless Finishing: Sharp corners make painting and staining easier and more uniform.
Essential Tools and Materials
To sharpen corner wooden moulding effectively, you’ll need the following tools:
Tools:
- Miter saw
- Coping saw
- Sanding block or electric sander
- Wood glue
- Clamps
- Utility knife
- Measuring tape
- Wood filler
- Fine-grit sandpaper (120 to 220 grit)
Materials:
- Wooden moulding pieces
- Finishing nails
- Wood filler
- Paint or stain (optional)
Pro Tip: Ensure all tools are sharp and in good condition for precise cuts and smooth finishes.
Step 1: Measure and Mark Accurately
Accurate measurements are the foundation of sharp corners.
- Measure Twice: Measure the length and angles of the corner where the moulding will be installed.
- Mark with Precision: Use a pencil and straight edge to mark the cutting points on the moulding.
Tip: Mark the face side of the moulding to ensure cuts align properly.
Step 2: Make Precise Cuts
Using a Miter Saw:
A miter saw is essential for making accurate angled cuts.
- Set the Correct Angle: For inside corners, set the miter saw to 45 degrees. For outside corners, set it to 45 degrees in the opposite direction.
- Align the Moulding: Place the moulding flat against the fence of the saw.
- Make the Cut: Use a slow and steady motion to make the cut.
Safety Note: Always wear safety goggles and follow the manufacturer’s instructions when using power tools.
Using a Coping Saw:
For more complex or irregular corners, a coping saw is ideal.
- Cut the Profile: Follow the profile of the moulding with the coping saw to create a perfect fit.
- Test the Fit: Place the moulding piece against the wall to check the fit. Trim as needed.
Step 3: Test Fit and Adjust
Before attaching the moulding, test fit the pieces together at the corner.
- Check for Gaps: Look for any visible gaps between the moulding pieces.
- Make Adjustments: Use sandpaper or a utility knife to refine the edges and achieve a tight fit.
Tip: A small gap can be filled with wood filler, but a tight fit is always preferable.
Start Your Next Project With Teds’ Archive Of 16,000 Plans!
Instant access to all 16,000 woodworking plans with step-by-step details, photos, materials lists and more
Monthly free plans with lifetime membership access – No renewals, recurring fees or other charges
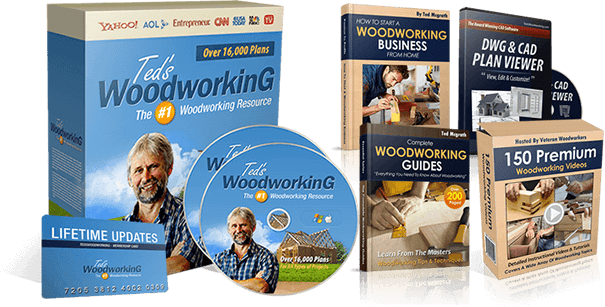

Step 4: Secure the Moulding
1. Apply Wood Glue:
- Apply a thin layer of wood glue to the edges of the moulding.
- Spread the glue evenly for maximum adhesion.
2. Nail the Moulding:
- Use finishing nails to secure the moulding to the wall.
- Drive the nails at an angle for better hold.
3. Clamp if Necessary:
- Use clamps to hold the moulding in place while the glue dries.
Tip: Countersink the nails slightly and fill the holes with wood filler for a clean finish.
Step 5: Sand and Smooth the Corners
- Use a Sanding Block:
- Sand the corners gently to remove rough edges and achieve a smooth finish.
- Start with 120-grit sandpaper and progress to 220-grit for a polished surface.
- Check for Smoothness:
- Run your hand over the corner to ensure it feels smooth.
Tip: Sand in the direction of the wood grain to avoid scratches.
Step 6: Fill and Finish
1. Apply Wood Filler:
- Fill any small gaps or imperfections with wood filler.
- Smooth the filler with a putty knife and let it dry completely.
2. Sand Again:
- Lightly sand the filled areas to ensure a seamless surface.
3. Apply Finish:
- Paint or stain the moulding as desired.
- Apply multiple coats for a rich and durable finish.
Pro Tip: Use painter’s tape to protect adjacent surfaces during finishing.
Expert Tips for Perfect Corners
- Use Scrap Pieces for Practice: Test your cuts on scrap pieces before cutting the actual moulding.
- Invest in Quality Tools: High-quality tools provide cleaner and more accurate cuts.
- Be Patient: Precision takes time. Rushing can lead to mistakes.
- Maintain Sharp Blades: Dull blades can cause splintering and uneven cuts.
Quote: “A well-crafted corner is the hallmark of professional woodworking.”
Common Mistakes to Avoid
1. Incorrect Angle Settings
Always double-check the miter saw angle before making cuts.
2. Skipping the Test Fit
Never skip the test fit step. It’s crucial for identifying and correcting gaps.
3. Inconsistent Sanding
Uneven sanding can lead to visible imperfections.
4. Overapplying Wood Filler
Use only enough filler to fill gaps. Excess filler can be difficult to sand.
FAQs
1. What is the best tool for cutting wooden moulding corners?
A miter saw is the best tool for precise angled cuts. A coping saw is useful for intricate profiles.
2. How do I fix gaps in moulding corners?
Use wood filler to fill small gaps and sand smooth. For larger gaps, re-cut the moulding.
3. Can I use adhesive instead of nails to secure moulding?
Yes, but nails provide better long-term stability.
4. How do I achieve a seamless finish?
Sand thoroughly, fill gaps with wood filler, and apply multiple coats of finish.
5. What type of wood is best for moulding?
Hardwoods like oak and maple are durable and offer a beautiful finish.
Conclusion
Sharpening corner wooden moulding like a pro requires precision, patience, and the right techniques. By following this step-by-step guide and incorporating expert tips, you can achieve professional-quality results that enhance the beauty and value of your woodworking projects. Happy crafting!
Sharpen Corner Wooden Moulding Like a Pro with These Simple Tips
How to Cut Tempered Glass Safely and Accurately
Creating a Perfect Mitered Box: A Beginner’s Guide to Precision Cuts
Best Dividers for Spice Drawer Organization and Efficiency
Step-by-Step Guide to Crafting a Perfect Woodworking Chest of Drawers